Unlocking the Future of Metal Fabrication with 3D Print Prototypes
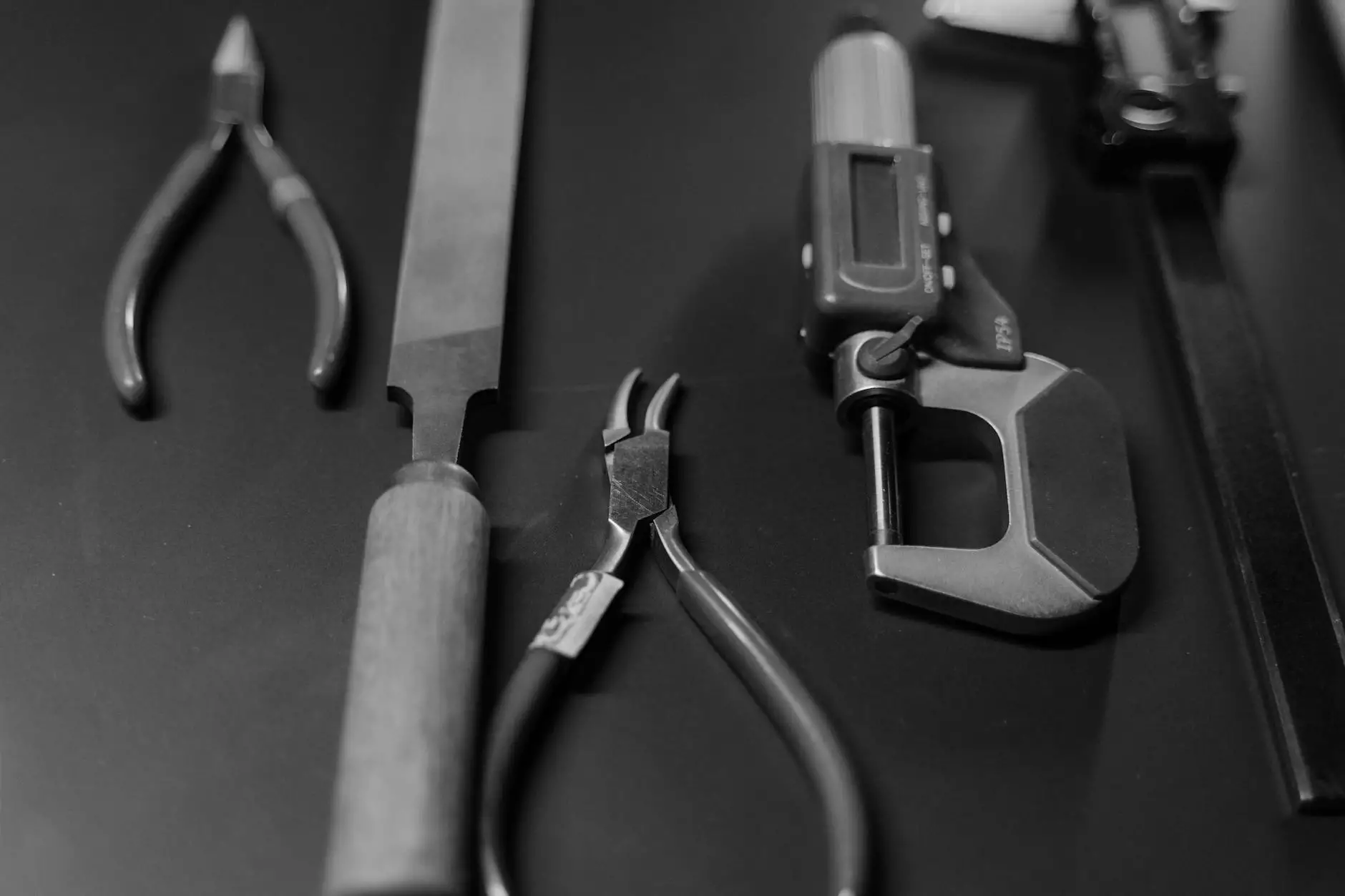
In today's fast-paced industrial landscape, innovation is not just a luxury; it's a necessity. The rise of 3D print prototypes has revolutionized the way metal fabricators approach their projects, enabling faster design iterations, cost-effective production, and unprecedented creativity. In this comprehensive guide, we will explore how 3D printing technology is reshaping the metal fabrication industry, examining its benefits, applications, and future trends.
The Importance of Prototyping in Metal Fabrication
Prototyping is a critical phase in the product development cycle, allowing businesses to test ideas before settling on the final design. The metal fabrication industry has traditionally relied on subtractive manufacturing methods, which can be time-consuming and costly. However, the advent of 3D print prototypes offers a solution that significantly enhances the prototyping process.
Key Benefits of 3D Print Prototypes
- Cost Efficiency: 3D printing reduces material waste and lowers production costs, making it an attractive option for fabricators.
- Speed: Designers can create and modify prototypes in a fraction of the time compared to traditional methods, allowing for quicker testing and iteration.
- Design Complexity: 3D printing allows for the creation of intricate designs that would be impossible or too expensive to achieve with traditional machining.
- Customization: Prototypes can be easily tailored to meet specific client needs or design specifications, enhancing product relevance.
- Reduced Lead Time: Faster prototyping means shorter time-to-market for new products, which can be a significant competitive advantage.
How 3D Print Prototypes Work in Metal Fabrication
The process of creating a 3D print prototype in the context of metal fabrication generally involves several systematic steps:
1. Conceptualization
The initial phase involves brainstorming and sketching ideas. Designers conceptualize the product while considering functional requirements and constraints.
2. CAD Modeling
Next, designers use Computer-Aided Design (CAD) software to create a detailed digital model of the prototype. This model serves as the foundation for the 3D printing process.
3. Preparation for Printing
The CAD model undergoes slicing, where it is divided into thin horizontal layers. This transformation ensures that the printer can effectively construct the model layer-by-layer.
4. Printing
The 3D print prototype is then created using various metal materials such as steel, aluminum, or titanium, depending on the application. The most common techniques for metal 3D printing include:
- Selective Laser Melting (SLM): Uses a laser to fuse metallic powders layer by layer.
- Electron Beam Melting (EBM): Similar to SLM but uses an electron beam instead of a laser.
- Binder Jetting: Involves binding metal powders with a polymer or adhesive to create the prototype.
5. Post-Processing
After printing, the 3D print prototype typically requires post-processing procedures, which may include heat treatment, surface finishing, and machining to achieve the desired specifications.
Applications of 3D Print Prototypes in Metal Fabrication
The versatility of 3D print prototypes opens up a myriad of applications across various industries:
Aerospace Industry
In aerospace, every gram counts. The ability to produce lightweight yet strong components using 3D printing is invaluable. Prototyping parts such as brackets, housings, and engine components allows manufacturers to reduce weight and improve fuel efficiency.
Automotive Industry
The automotive sector benefits significantly from 3D print prototypes by enabling rapid prototyping of parts for testing and validation. This method allows for custom designs that can meet specific performance criteria, driving innovation in car design.
Medical Applications
From bespoke implants to surgical instruments, the medical field utilizes 3D printing for producing custom prototypes that cater specifically to patient needs, enhancing both comfort and performance.
Tooling and Manufacturing
Manufacturers are using 3D print prototypes to create tooling components such as molds and fixtures, which significantly reduces lead time and costs. This flexibility allows for easier adaptations and adjustments during the production process.
Challenges and Considerations in 3D Metal Printing
While the benefits of using 3D print prototypes in metal fabrication are extensive, there are challenges that businesses must navigate:
Material Limitations
Not all metals are suitable for 3D printing. Understanding material properties is crucial for determining the right metal for each application.
Design Constraints
Though 3D printing allows for complex geometries, certain designs may present challenges during the printing process, necessitating adjustments to ensure successful production.
Post-Processing Requirements
3D printed metal parts often require extensive post-processing to achieve desired surface finishes or mechanical properties, which can increase production time and costs.
Future Trends in 3D Print Prototyping for Metal Fabrication
As technology continues to evolve, the future of 3D print prototypes in metal fabrication looks promising. Here are some anticipated advancements:
- Improved Materials: Continued research will likely lead to the development of advanced metal alloys that enhance the properties of 3D printed prototypes.
- Automation: The integration of AI and automation will streamline the prototyping process, leading to faster production and improved quality control.
- Increased Accessibility: As 3D printing technology becomes more widespread, small and medium-sized enterprises will increasingly adopt 3D print prototypes for their own fabrication needs.
- More Sustainable Practices: Innovations in eco-friendly printing materials and practices will help reduce the environmental impact of metal fabrication.
Conclusion
In conclusion, 3D print prototypes are revolutionizing the metal fabrication industry. From cost and time efficiency to fostering innovation, the implications of this technology are profound. As businesses continue to embrace these transformational practices, we can expect to see significant advancements that will shape the future of manufacturing. The road ahead is promising, and companies that leverage 3D printing technology will undoubtedly gain a competitive edge in the marketplace.
For businesses looking to adapt and excel in this evolving landscape, investing in 3D print prototypes is a strategic move that offers long-term benefits and a pathway to success.