CNC Machine Precision: Revolutionizing Metal Fabrication
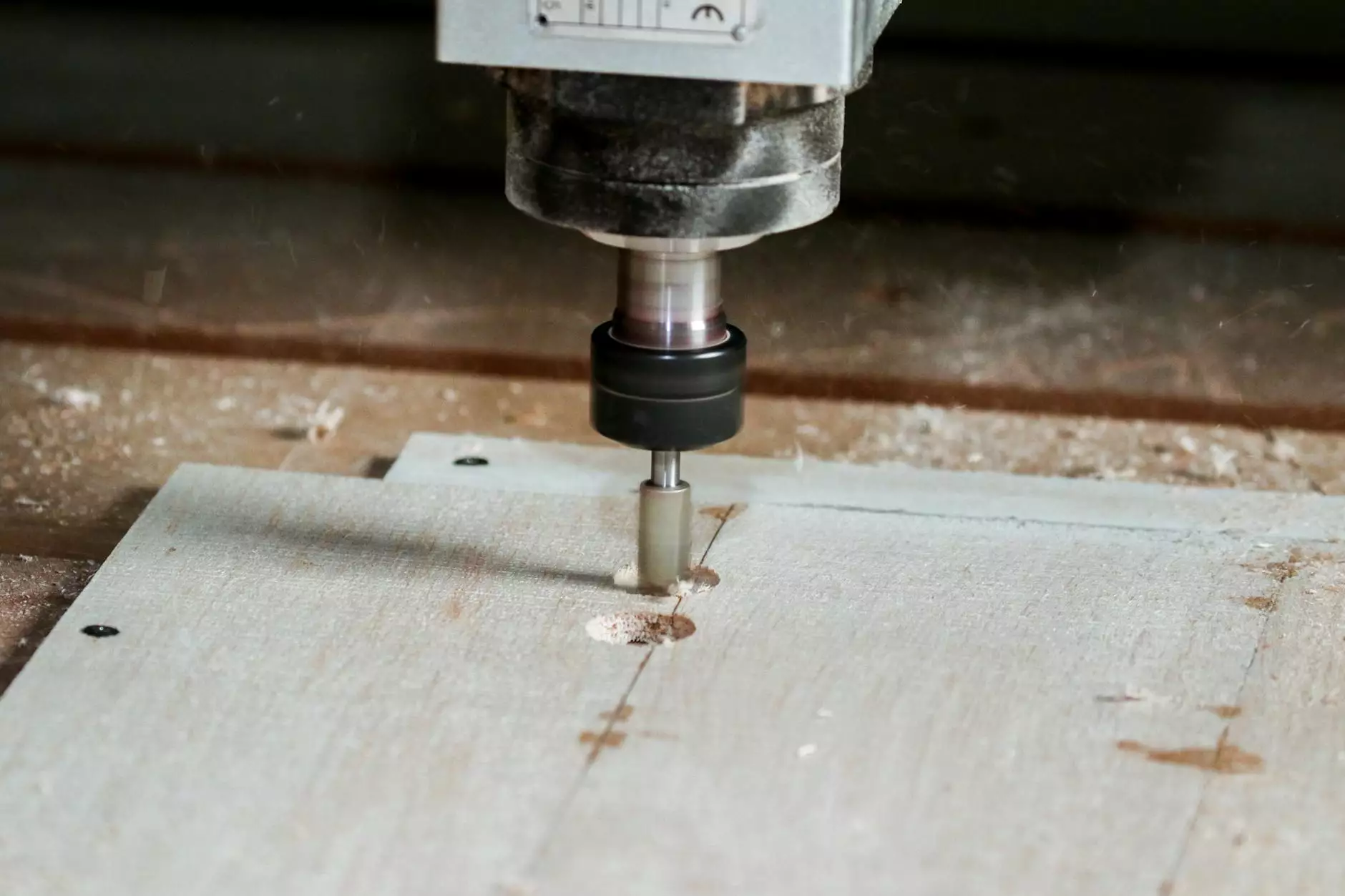
The advent of CNC (Computer Numerical Control) technology has dramatically transformed the landscape of manufacturing, particularly in the realm of metal fabrication. The phrase “cnc machine precision” encapsulates the heart of this technological revolution. This article delves deep into how CNC machines enhance the precision of metal fabrication, exploring their advantages, applications, and the future of CNC technology.
Understanding CNC Machines
CNC machines are sophisticated automated systems that utilize computer programming to control machinery and tools in the manufacturing process. Unlike traditional manual machining methods, CNC machines operate on a set of pre-programmed instructions, ensuring consistent and repeatable results. This precision is vital in metal fabrication, where even the slightest deviation can lead to flawed products.
Components of CNC Machines
- Computer Control Unit: This serves as the brain of the CNC machine, interpreting the CAD (Computer-Aided Design) models.
- Machine Tool: The physical apparatus that performs the machining tasks such as lathes, mills, routers, and plasma cutters.
- Servo Motors: These provide the necessary power and torque to move the machine components accurately.
- Feedback Systems: Essential for monitoring the movement and position of the machine tool, ensuring continued accuracy.
The Importance of CNC Machine Precision in Metal Fabrication
Precision in metal fabrication is crucial for several reasons:
- Quality Assurance: High precision ensures that parts meet specifications, resulting in reduced scrap rates and higher quality end products.
- Efficiency: CNC machines can operate continuously, reducing the time spent on producing complex components.
- Cost-Effectiveness: The reduction in material waste and rework translates into significant cost savings.
- Flexibility: CNC machines can be quickly reprogrammed for different jobs, making them adaptable to varying production needs.
Benefits of CNC Machine Precision
Investing in CNC technology brings various benefits that make it an indispensable tool in modern metal fabrication processes:
1. Enhanced Accuracy and Consistency
CNC machine precision guarantees that each piece produced is identical to the last. This level of accuracy is unattainable with manual machining, where human error can lead to significant variances.
2. Complex Geometries Made Simple
CNC machining excels at producing complex shapes and intricate designs that would be time-consuming or impossible with traditional manufacturing methods. For instance, creating 3D geometries or components with tight tolerances becomes feasible and efficient.
3. Reduction in Production Time
Automating the machining process significantly reduces production times, enabling businesses to fulfill large orders faster without compromising quality. This efficiency is paramount in industries where time-to-market is critical.
4. Improved Worker Safety
By minimizing human involvement in the machining process, CNC technology enhances workplace safety. Operators can control machines from a distance, reducing the risk of injuries associated with manual handling of heavy equipment.
Applications of CNC Machine Precision
The versatility of CNC machines means they are employed across various sectors. Here are some prominent applications:
1. Aerospace Industry
The aerospace sector relies heavily on CNC machining to produce parts that require exact dimensions and tolerances. From aircraft frames to turbine components, the precision of CNC machining ensures safety and reliability in air travel.
2. Automotive Manufacturing
CNC machine precision is vital in automotive production, from creating engine blocks to intricate interior components. The automotive industry benefits from both the cost efficiency and the accuracy that CNC technology offers.
3. Medical Devices
The medical field demands high-stakes precision. CNC machining is used to manufacture surgical instruments, orthopedic implants, and custom prosthetics, where errors can have serious consequences.
4. Electronics
CNC machines create intricate circuit boards and enclosures for electronic equipment, ensuring functionality and aesthetic appeal. The precision that CNC offers is vital for the performance and assembly of electronic devices.
The Future of CNC Machine Precision
As technology advances, the capabilities of CNC machines will continue to evolve, providing even greater levels of precision and automation. Here are a few trends to watch:
1. Integration with AI and Machine Learning
Future CNC systems may incorporate artificial intelligence to optimize machining operations continuously. AI can analyze data in real-time and adjust parameters for improved efficiency and quality.
2. Increased Use of Robotics
The combination of CNC technology with robotics is expected to streamline operations further. Robots can handle materials, load/unload parts, and even assist in complex machining tasks, enhancing both speed and safety.
3. Sustainable Manufacturing
The push for environmentally friendly practices will influence CNC machining innovations. Techniques that reduce waste, energy consumption, and material usage will likely gain traction as sustainability becomes a priority in manufacturing.
Conclusion: The Unmatched Value of CNC Machine Precision
In conclusion, the phrase “cnc machine precision” represents a cornerstone of modern metal fabrication. The ability to produce parts with unparalleled accuracy not only enhances the quality of products but also maximizes efficiency and safety across various industries. As technology continues to evolve, CNC machines will undoubtedly play a vital role in shaping the future of manufacturing.
For companies like Deep Mould in the metal fabrication category, embracing CNC technology is not just an option—it's a necessity to remain competitive in an ever-evolving market. With the increasing demand for high-quality, precision-engineered components, investing in CNC machine precision is the key to business success and growth.