Hydraulic Tube Fittings Manufacturer: Premium Quality for Every Application
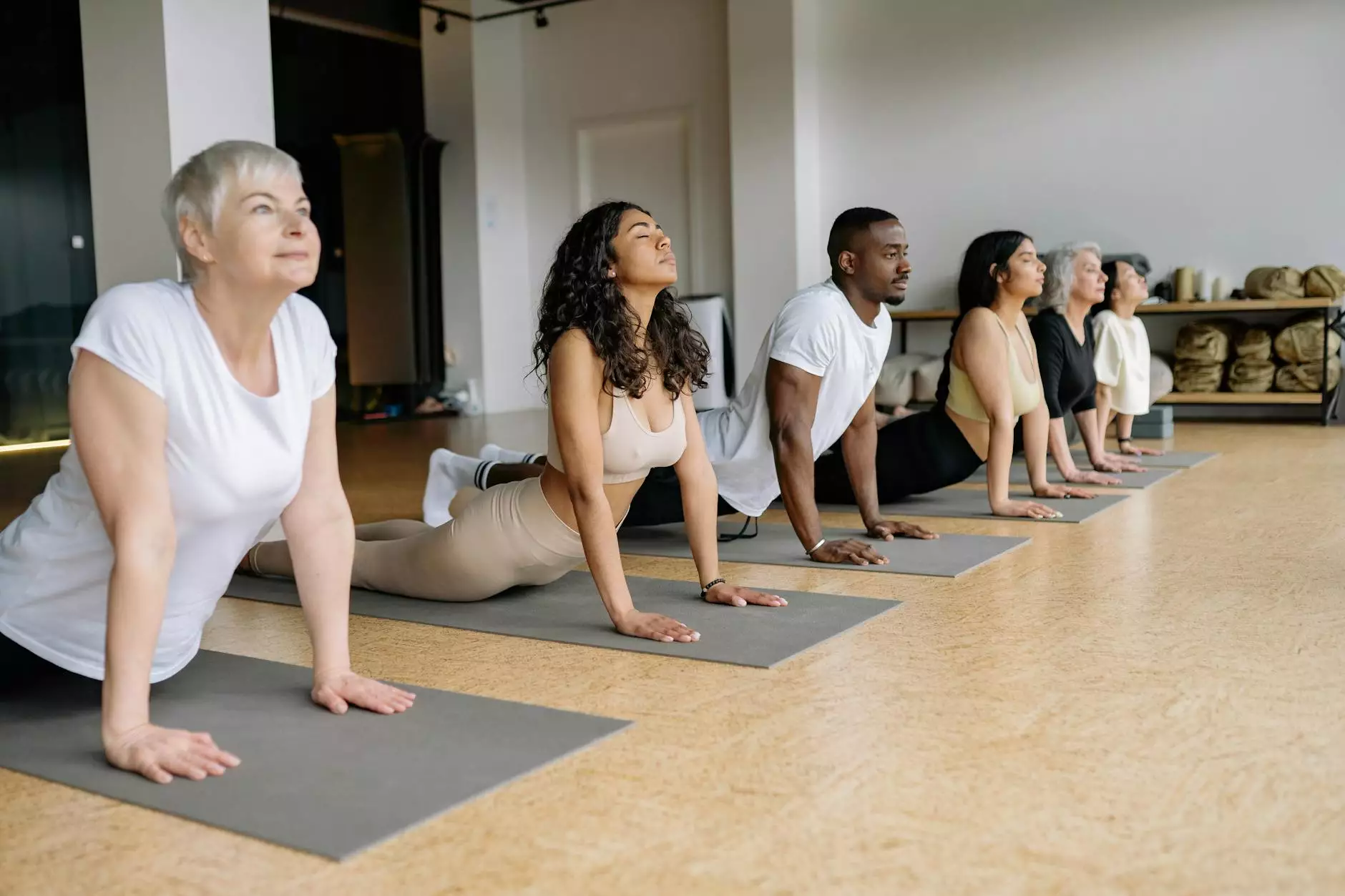
Understanding Hydraulic Tube Fittings
Hydraulic tube fittings are critical components in hydraulic systems, ensuring the secure connection of pipes and tubes in various machinery and equipment. These fittings play an essential role in preventing leaks and maintaining system integrity, making them indispensable in industries ranging from construction to manufacturing.
What Are Hydraulic Tube Fittings?
Hydraulic tube fittings consist of various components, including nuts, sleeves, and connectors, which work together to create a tight seal on hydraulic tubes. These fittings come in numerous shapes and sizes, each tailored for specific applications and pressures.
Types of Hydraulic Tube Fittings
There are several types of hydraulic tube fittings, each designed to serve different purposes. The most common types include:
- Compression Fittings: These fittings use a compression mechanism to seal the connection, making them ideal for applications requiring high-pressure resistance.
- Flared Fittings: Featuring a flared end, these fittings provide a secure connection by creating a wider contact area against the tube.
- Socket Weld Fittings: Often used in high-pressure systems, socket weld fittings are directly welded onto the pipe for enhanced durability.
- Threaded Fittings: Utilizing threaded connections, these fittings are easy to install and uninstall, providing flexibility in hydraulic systems.
Applications of Hydraulic Tube Fittings
Hydraulic tube fittings find applications across various sectors, including:
- Manufacturing: Used in hydraulic machinery to control movement and pressure.
- Aerospace: Critical for hydraulic systems in aircraft for safe and precise operation.
- Construction: Integral in heavy machinery such as excavators and bulldozers.
- Automotive: Essential for the operation of hydraulic brakes and steering systems.
Why Choose a Leading Hydraulic Tube Fittings Manufacturer?
Selecting a reliable hydraulic tube fittings manufacturer is paramount for the success of your projects. Here are several reasons to partner with a top-tier manufacturer, such as fitsch.cn.
Quality Assurance
The best hydraulic tube fittings manufacturers adhere to strict quality control processes. They ensure that every fitting produced meets international standards, thereby minimizing the risk of failure under pressure.
Customized Solutions
Top manufacturers offer customized fittings tailored to meet specific project requirements. This customization can enhance performance and efficiency, ensuring that your hydraulic systems operate flawlessly.
Comprehensive Product Range
A leading manufacturer will provide a diverse range of fittings, catering to various industries' needs. From basic fittings to complex assemblies, having a supplier that offers extensive options can simplify procurement processes.
Technical Expertise
With years of experience in the industry, reputable manufacturers have the technical knowledge necessary to assist clients in selecting the right fittings for their applications. This expertise helps avoid costly mistakes and ensures optimal performance.
Post-Sales Support
Dependable manufacturers often offer after-sales service, helping clients with installation guidance, troubleshooting issues, and maintenance advice, ensuring the longevity of the fittings and client satisfaction.
The Manufacturing Process of Hydraulic Tube Fittings
Understanding the manufacturing process of hydraulic tube fittings can provide insights into their quality and reliability. The process typically involves several key stages:
Design and Engineering
The design phase involves engineers determining the specifications of the fittings based on their intended application. This phase includes material selection, size, and pressure requirements.
Raw Material Selection
High-quality raw materials, such as stainless steel, brass, and carbon steel, are selected for durability and resistance to corrosion and wear. The choice of material has a direct impact on the fitting's lifespan and performance.
Manufacturing Techniques
Common techniques used in the manufacturing of hydraulic tube fittings include:
- CNC Machining: Provides precision in manufacturing, ensuring a perfect fit and adherence to specifications.
- Stamping: Efficiently produces a large volume of parts with consistent quality.
- Forging: Enhances the strength of fittings by altering the metal structure through high-pressure techniques.
Quality Testing
Once the fittings are manufactured, they undergo rigorous testing to ensure they can withstand specified pressures and conditions. This testing may include:
- Hydraulic Pressure Testing: To test for leaks and the ability to handle high pressure.
- Dimensional Inspection: To verify that each fitting meets the required specifications.
- Material Testing: To ensure the integrity and strength of the raw materials used.
Choosing the Right Hydraulic Tube Fittings
Selecting the right hydraulic tube fittings is crucial for ensuring efficiency and safety in hydraulic systems. Here are some key factors to consider:
Material Compatibility
It's essential to select fittings made from materials that are compatible with the fluids being transported. For example, fittings that will be exposed to corrosive environments should be made from resistant materials such as stainless steel.
Pressure Ratings
Every hydraulic system operates under specific pressure ratings. It is vital to choose fittings that can handle the maximum pressure of your application to prevent failures and ensure safety.
Size and Threading
Ensure that the fittings' size and threading match those of your hydraulic system. Incorrect sizing can lead to leaks and system inefficiencies.
Temperature Resistance
Select fittings that can withstand the temperature conditions of your hydraulic system. High temperatures can weaken materials and compromise connections.
The Future of Hydraulic Tube Fittings
The hydraulic fittings industry is evolving, with advancements in technology driving innovation. Here are some trends to watch:
Smart Hydraulics
With the rise of Industry 4.0, smart hydraulic systems that incorporate IoT sensors are being developed. These systems can monitor pressure, flow rate, and temperature in real-time, enhancing efficiency and safety.
Eco-Friendly Materials
As industries become more environmentally conscious, manufacturers are exploring the use of eco-friendly materials for hydraulic tube fittings, reducing environmental impact without compromising performance.
Improved Manufacturing Techniques
Innovations in manufacturing processes, such as additive manufacturing (3D printing), are set to revolutionize how hydraulic fittings are produced, offering greater customization and reducing waste.
Conclusion: Your Trusted Hydraulic Tube Fittings Manufacturer
In summary, partnering with a reputable hydraulic tube fittings manufacturer like fitsch.cn offers numerous advantages. From high-quality products to exceptional customer service, industry leaders ensure that you receive the best fittings for your hydraulic systems. With the right fittings, you can enhance the performance and safety of your operations, paving the way for success in your business ventures.
Hydraulic Tube Fittings Manufacturer